鋰輝石生產碳酸鋰前段工藝:鋰輝石礦石制取硫酸鋰鹵水說明
鋰輝石生產碳酸鋰包括前期焙燒制鹵水及鹵水生產碳酸鋰兩個相對獨立的環(huán)節(jié)。鋰輝石制取鹵水又包括烘干-焙燒-冷卻-破碎-粉磨-酸化-水浸-固液分離共八個小環(huán)節(jié)。
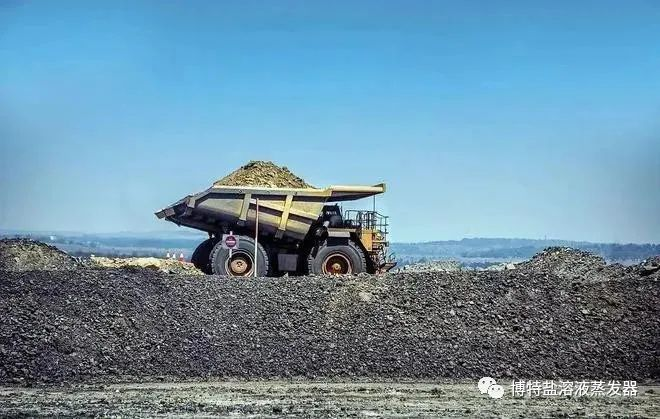
澳洲鋰輝石
一、烘干:項目購入的鋰輝石含水率通常為8%,為了不影響后續(xù)焙燒過程,需對物料進行烘干處理,烘干在回轉式干燥窯內進行,烘干溫度約為250℃,持續(xù)時間約15min,熱風與物料直接接觸。烘干后鋰輝石含水率約6.5%,同時烘干過程可減少后續(xù)焙燒過程的燃氣量。干燥熱源來自回轉窯尾氣余熱(為實現節(jié)能降耗,一部分回轉式焙燒窯尾氣余熱約250℃的熱煙氣經風機引至干燥窯內)烘干的收集粉塵全部會用于焙燒工序。
二、焙燒:烘干完成后的鋰輝石經窯尾進入焙燒回轉窯高溫焙燒室焙燒(以焦爐煤氣為燃料,在隧道式焙燒窯中段設置噴槍直接燃燒),回轉窯采用焦爐煤氣作為燃料,通過直接加熱的方式對原材料進行高溫焙燒,其控制燒結溫度為1100~1200℃,焙燒時間持續(xù)約2h。
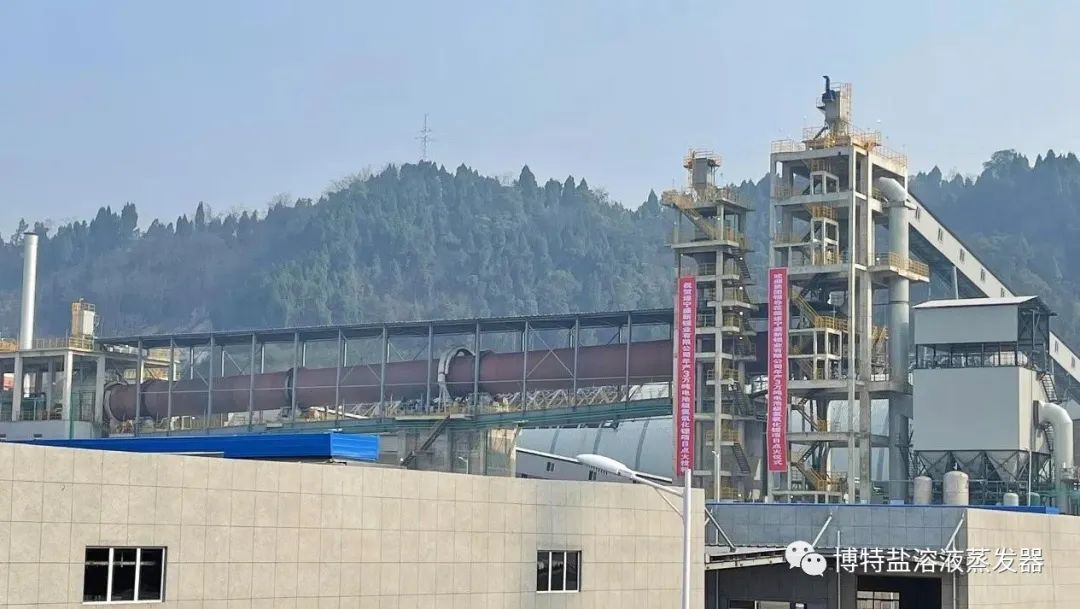
回轉窯
焙燒完成后鋰輝石原料由α型鋰輝石轉為β型鋰輝石,使得鋰從不溶于酸的結構轉化為可溶于酸的結構,轉化率為95-98%。
轉型過程方程式為:α-Li2O·Al2O3·4SiO2→β-Li2O·Al2O3·4SiO2
三、冷卻:物料在高溫焙燒時,由于部分物料熔融,燒結出來的物料會有一定的強度,需對其進行冷卻,進入冷卻窯經強制風冷降溫至90℃左右。焙燒后的冷卻時間為1.5小時。
四、破碎:冷卻后的熟料使用封閉式鏈斗輸送機傳送至破碎機進行破碎,以防止有大塊熟料進入后續(xù)工序,破碎至10mm左右粒度,熟料經過封閉式皮帶運輸機輸入立磨系統(tǒng)之中。
五、粉磨:為便于后續(xù)的浸出作業(yè),使熟料溶解更充分,破碎后的熟料需進一步粉磨。物料通過入磨皮帶計量秤將其送入立磨系統(tǒng)磨盤上,在離心力的作用下,物料向磨盤的周緣移動。當物料通過磨盤和磨輥之間時,在壓緊力的作用下受到擠壓和碾磨而被粉碎成粉末。已磨成的物料粉顆粒繼續(xù)向外移動,最后拋向磨盤周緣;依靠主排風機抽力形成的負壓,微熱的干燥劑氣體從立磨進風口進入磨機并通過磨盤外緣自下而上;物料粉顆粒被微熱的干燥劑氣體攜帶上升,在分離器內較重的粗大物料粉顆粒碰撞在分離器的葉片擋板上返回磨盤再研磨;較輕的細小物料粉顆粒通過分離器被收粉器收集;立磨上部的分離器裝置對研磨后的物料進行篩分,細度不合格的物料粉沿著內錐體內壁從旋流中被分離并返回磨盤上繼續(xù)研磨。粉磨后的物料粒徑在100目以下進入下一工序。
六、酸化:粉碎至100目以下的β型鋰輝石與98%濃硫酸在混料機上混合酸化(比例為2.5-3.5:1),混合料通過進料螺旋輸送機輸送至2臺酸化窯,酸化窯采用燃燒焦爐煤氣的熱風爐供熱,采用外熱式間接加熱方式加熱,控制反應溫度為250~300℃,持續(xù)時間約10min,β型鋰輝石會與硫酸充分發(fā)生鹽化反應,反應方程式如下:
Li2O·Al2O3·4SiO2 +H2SO4→Li2SO4 + H2O·Al2O3·4SiO2
同時也發(fā)生如下副反應:
Na2O·Al2O3·4SiO2 + H2SO4→Na2SO4 + H2O·Al2O3·4SiO2
K2O·Al2O3·4SiO2 +H2SO4→ K2SO4 + H2O·Al2O3·4SiO2
MgO·Al2O3·4SiO2+H2SO4→ MgSO4 + H2O·Al2O3·4SiO2
CaO·Al2O3·4SiO2+ H2SO4→ CaSO4 + H2O·Al2O3·4SiO2
Fe2O3 +3H2SO4→Fe2(SO4)3 +3H2O
ZnO + H2SO4→ZnSO4 + H2O
TlO2+ H2SO4→TlOSO4+ H2O
在物料發(fā)生鹽化反應時,鋰輝石的鋁硅酸鹽核和硫酸之間發(fā)生了樹脂除雜,交換的結果使鋰輝石中的鋰被氫置換,而礦物結構實際上并未破壞。鹽化反應完成的酸化料由螺旋輸送機送入冷卻窯,經過間接水冷冷卻至80℃以下,再進入后續(xù)浸出工序。
酸化焙燒裝置設計分為4個部分:原料單元、酸化焙燒單元、冷卻儲存單元、供熱單元等內容。
(1)原料單元
①細焙燒料鋰輝石下料、稱重計量工序。
細焙燒料倉里的β鋰輝石進入本單元內,通過密閉式稱重給料機稱重計量后,投入雙螺旋混料器。
②濃硫酸輸送、計量工序。
濃硫酸由廠區(qū)硫酸罐區(qū)采用管道輸送進入計量罐,經硫酸投料泵送至雙螺旋混料器。
(2)酸化焙燒單元
①β鋰輝石細粉(100目)從細粉料倉底部出口,自流入計量秤。
②計量稱一般采用螺旋秤、轉子秤、科里奧力秤等,本項目采用科里奧力秤。
③計量秤出口接螺旋輸送機,通過科里奧力秤的讀數,控制螺旋輸送機的轉速,從而控制鋰輝石粉送料量。
④螺旋輸送機出口接混料機。
⑤混料機一般采用單螺旋混料機、螺帶混料機、雙螺旋混料機。本項目采用雙螺旋混料機。
⑥98%硫酸從儲罐通過襯氟磁力泵,送入混料機。
⑦硫酸管道上設置流量計和調節(jié)閥。
⑧通過鋰輝石質量流量控制硫酸的質量流量。
⑨硫酸通過多點噴頭噴入混料機,與鋰輝石細粉進行機械混合,混合物稱為混酸料。
⑩混酸料再通過進窯螺旋,經窯尾罩送入酸化窯。
(3)酸化熟料冷卻儲存單元
從爐尾出來的酸化料由螺旋送入冷卻窯冷卻至80℃以下,冷卻窯采用冷凍水間接冷卻的形式,冷卻后的酸化熟料送廠內濕法工段。
(4)供熱單元
本項目供熱系統(tǒng)選用燃焦爐煤氣熱風爐供應熱風循環(huán)系統(tǒng)(熱風循環(huán)使用)的形式。
由管道送來的焦爐煤氣與空氣風機送來的經預熱的空氣在熱風爐中燃燒,燃燒產生的熱煙氣在熱風爐的尾段與高溫循環(huán)風機送來的循環(huán)熱煙氣進行混合,由熱風管道經閥門調控后進入酸化窯的夾套為爐體供熱。熱煙氣大部分在供熱系統(tǒng)內進行循環(huán),一部分預熱空氣后,由煙囪排空。系統(tǒng)中各路風管均設置有調節(jié)門,可以實現爐體各段加熱溫度的不同要求。排煙道設置調節(jié)閥,用于調節(jié)系統(tǒng)風壓的平衡。
操作條件和控制參數:控制反應溫度為250℃~300℃,硫酸的投料量根據礦石中有效成分Li2O的量確定,保持拌酸料中游離酸含量為20-22%,由此確定的料酸比約為2.5-3.5,物料在焙燒爐中的停留時間約為30min。酸熟料中游離酸含量為2-6%,常壓。
七、水浸:酸化冷卻后的鋰輝石酸熟料中約含2~6%的硫酸,經酸熟料倉由埋刮板輸送機送入打漿罐內,并用鋰渣洗液、樹脂再生出水和冷凝水按約1.6:1左右的液固比配成酸性的酸熟料漿(酸熟料冷卻后溫度約在40℃,經下料通道進入封閉式浸出槽液面以下)后送入中和槽,再加入石灰石、生石灰對殘留的硫酸進行中和。石灰石、生石灰由給料機經埋刮板輸送機輸入中和槽,中和槽內的pH計控制給料機轉速,進而控制石灰石、生石灰的加入量。當pH達到6~6.5之后,停止加料,中和反應持續(xù)20min。浸出完成后鋰由固相進入液相(中和料漿),鋰浸出率達98%左右。中和料漿由料漿泵送入壓濾機進行后續(xù)作業(yè)。
反應方程式:
CaCO3 +H2SO4→CaSO4 + CO2↑+H2O
CaO+H2SO4→CaSO4 +H2O
操作條件和控制參數:浸出溫度40℃,液固比1.6:1,浸出時間2~3h,常壓。
八、固液分離:
中和料漿泵入壓濾機后,經過過濾、洗滌、壓榨、吹風、卸渣等工序,分別得到濕鋰渣、硫酸鋰濾液、鋰渣洗液。
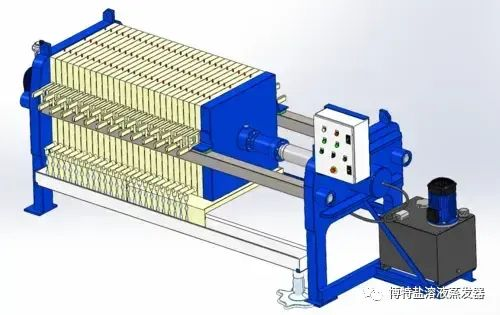
板框壓濾機
過濾:中和料漿泵入壓濾機進行固液分離,當料漿泵流量衰減至5m3/h左右時壓濾機停止進料,濾出濾液主要為硫酸鋰濾液,經濾液槽暫存后進入除雜工序。
洗滌:固廢分離所得濾渣中鋰含量仍然較高,通過冷凝水在線淋洗,以盡可能多的淋洗出鋰渣中的硫酸鋰溶液。淋洗所得溶液即為鋰渣洗液,返回浸出工序用于酸熟料配漿。
壓榨:淋洗完畢后的鋰渣繼續(xù)壓榨,壓出濾液返回浸出工序用于酸熟料配漿。
瀝干:壓榨完畢后的鋰渣采用0.7MPa的濕空氣吹風瀝水,瀝下水返回浸出工序用于酸熟料配漿。瀝干后的鋰渣含水率小于20%。
卸渣:利用皮帶運輸機將壓濾完成的浸出渣作為固廢處理。
鹽溶液蒸發(fā)器 轉載自博特鹽溶液蒸發(fā)器